Ultrasonic measurement is a non destructive method which is applied to measure thickness of a wide range of structures or components that includes ship hulls, piping, pressure vessels and structural steels etc.
An ultrasonic thickness gauge works on a sound pulse that has been generated by an ultrasonic transducer which travels through a test piece and reflect back from surface walls. Wave Travelling Time is then calculated accordingly and measured thickness is determined instantaneously.
Thickness Measurement provides important decisive parameters to ensure safety of inspected structures or components like for e.g. Analyzing metal loss caused by corrosion, erosion or damages etc in accord with original metal thickness during which it was designed. Also it works as decision making parameter for replacement or repairs of parts in structure or components.
Precision Thickness of Steels (M.S., S.S., C.S., C.I.), Aluminum, Copper, Lead, Tin, Other Metals Alloys, Brass, Monel, Specific Alloys, Glass, Ceramic etc. can easily be determined by Ultrasonic.
- Couplant is used for transmitting ultrasonic waves between probe and test piece.
- Incorrect selection of couplant may cause error.
- Couplant should be taken in adequate quantity and must adhere evenly to test surface.
- For Smooth surfaces low viscous couplant like Machine oil must be used and for rough surfaces high viscous couplant like gel, glycerine must be used.
- Ultrasonic rays do not penetrate properly through laminated, compounded or porous material so accurate measurement of their test piece is not possible.
- While measuring Super thin materials( Less than 4mm), the displayed reading might be as big as twice the actual thickness, this type of sensor limitation is known as “Dual Deflection “.
- Another similar limitation is known as “Pulse/ Cyclic jumping” which results in showing readings bigger than actual.
- For curved surfaces (in Steels) radius of test piece must be above 10mm and wall thickness must be above 3mm
- Surface Roughness, Rust and Eroded Pits may cause haywire readings. Under certain cases there might even be no readings.
- In order to obtain satisfactory results the other side of the test piece must be parallel or co axial with test surface. Else there will be erratic readings.
- Few metals like Aluminium has tendency of surface oxidation, due to which errors may occur.
EleWave Ultrasonic Thickness Gauge is on par in excellence to its direct competitors and import substitutes in terms of Quality, Serviceability and Precision.
EleWave Ultrasonic Thickness Gauge is completely Designed, Developed and Manufactured “Here In Bharat”. Rather than Re-branding or Re-assembling them in disguise as of “Made In India” after importing from other countries.
EleWave Ultrasonic Thickness Gauge
Innovative Features
- Complete Digital Circuit.
- Direct Measurement.
- Stable and Repeatable Readings.
- Highest Accuracy and Resolution.
- Advanced Calibration System.
- Inch/MM Converter.
- Resolution converter.
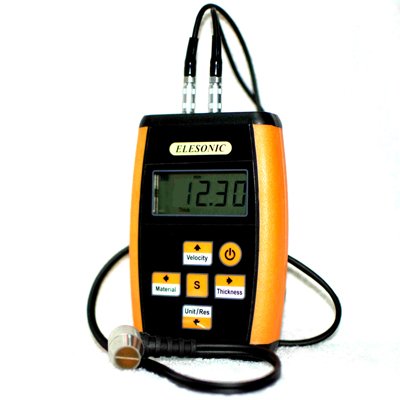
Probe Design
- LEMO type Connectors for accurate Signal Transmission.
- Highly Flexible Probe Cable with strain relief.
- Fully Metallic High Quality Probe for High Service life.
Ergonomics
- Compact and Light Weight Instruments.
- Full ABS high Impact resistant body.
- Attractive instrument display and visuals.
- External battery compartment.
Display
- Large High Contrast LCD Display.
- Sun Readable.
- Energy Efficient
Technical Specifications
Principle | Ultrasonic Pulse Echo |
Measurement Range | 1.2 mm to 300mm in Steel/M.S.* |
Resolution (MM) | 0-99.99=0.01,100-300=0.1 |
Accuracy | + 0.1mm < 60mm, + 1% > 60mm |
Calibration | Single Point Calibration |
Velocity Range | 1000 M/Sec to 9990 M/Sec |
Display | Large High Contrast LCD |
Battery Type | 9V (6F22) |
Operating Time | 50+ Hours ( With Alkaline Battery) |
Size | 117 mm (L) x 85mm (W) x 25mm (H) |
Weight | 400 Gms. (Including Batteries) |
Applicable Materials | Steel (M.S., S.S., C.S., C.I.), Aluminum, Copper, Lead, Tin, Other Metals, Brass, Monel, Specific Alloys, Glass, Ceramic etc.* |